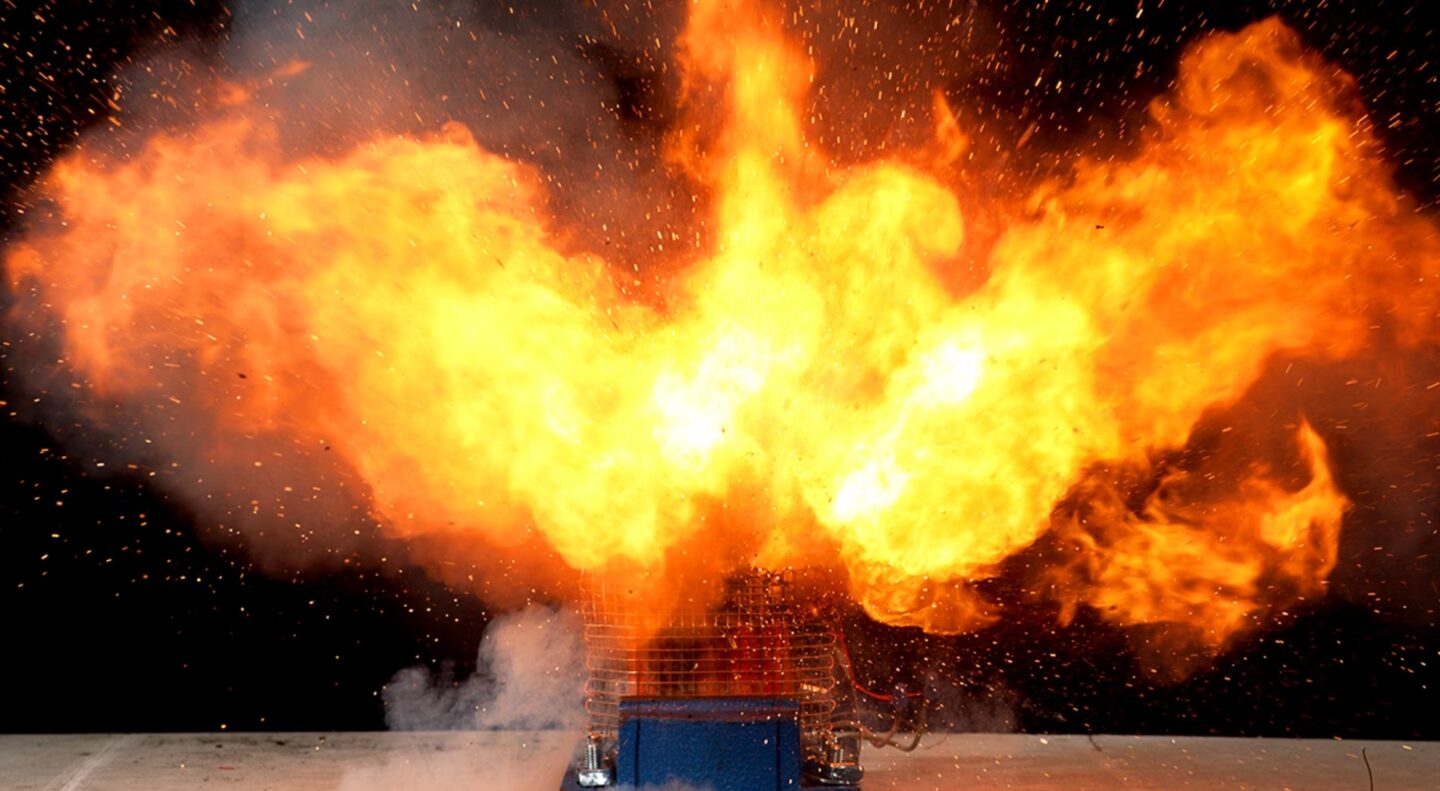
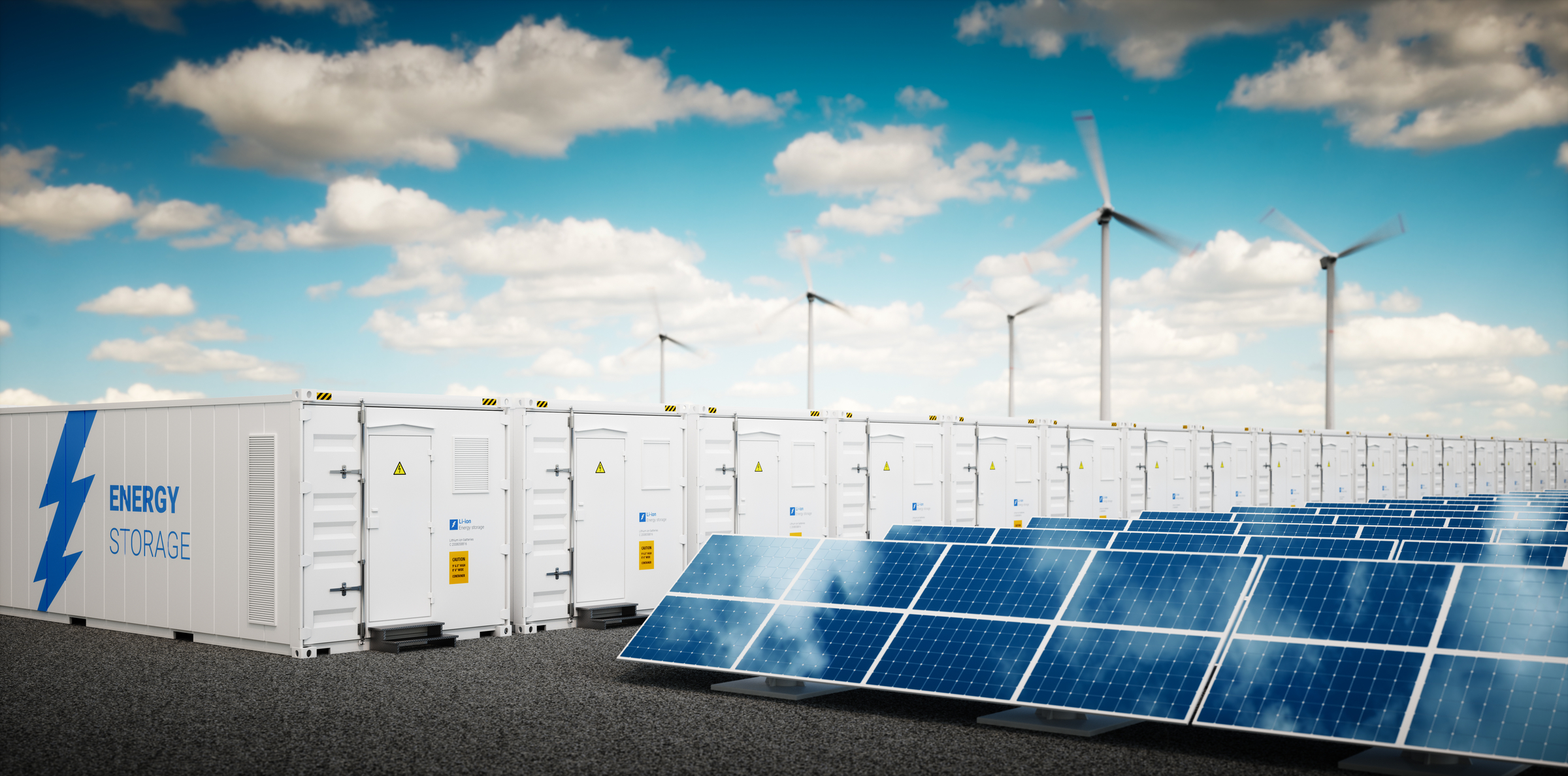
Electrochemical Safety Research Institute
Advancing safer design and deployment of energy storage and energy generation through science.
Renewable energy technologies are one of the highest priority solutions to climate change. Our scientists explore the safety and performance of batteries and other renewable energy technologies to lay the foundation for electrochemical energy storage that is reliable, sustainable, and safe.
Our Research
Our scientific research helps those in the energy storage and energy generation value chains understand safety and sustainability issues associated with battery chemistries and applications, hydrogen generation and transportation, and other energy solutions.
Research initiatives
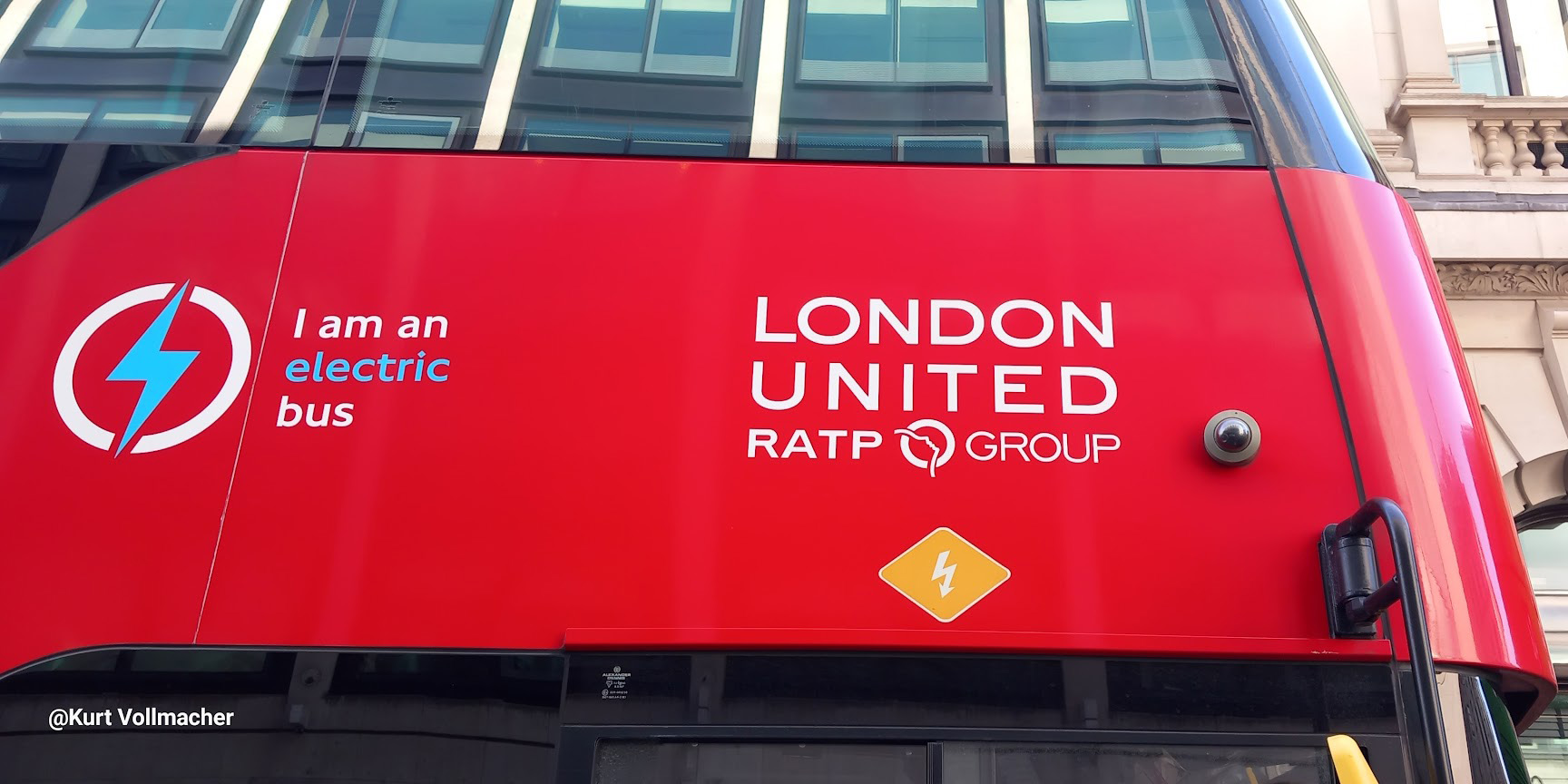
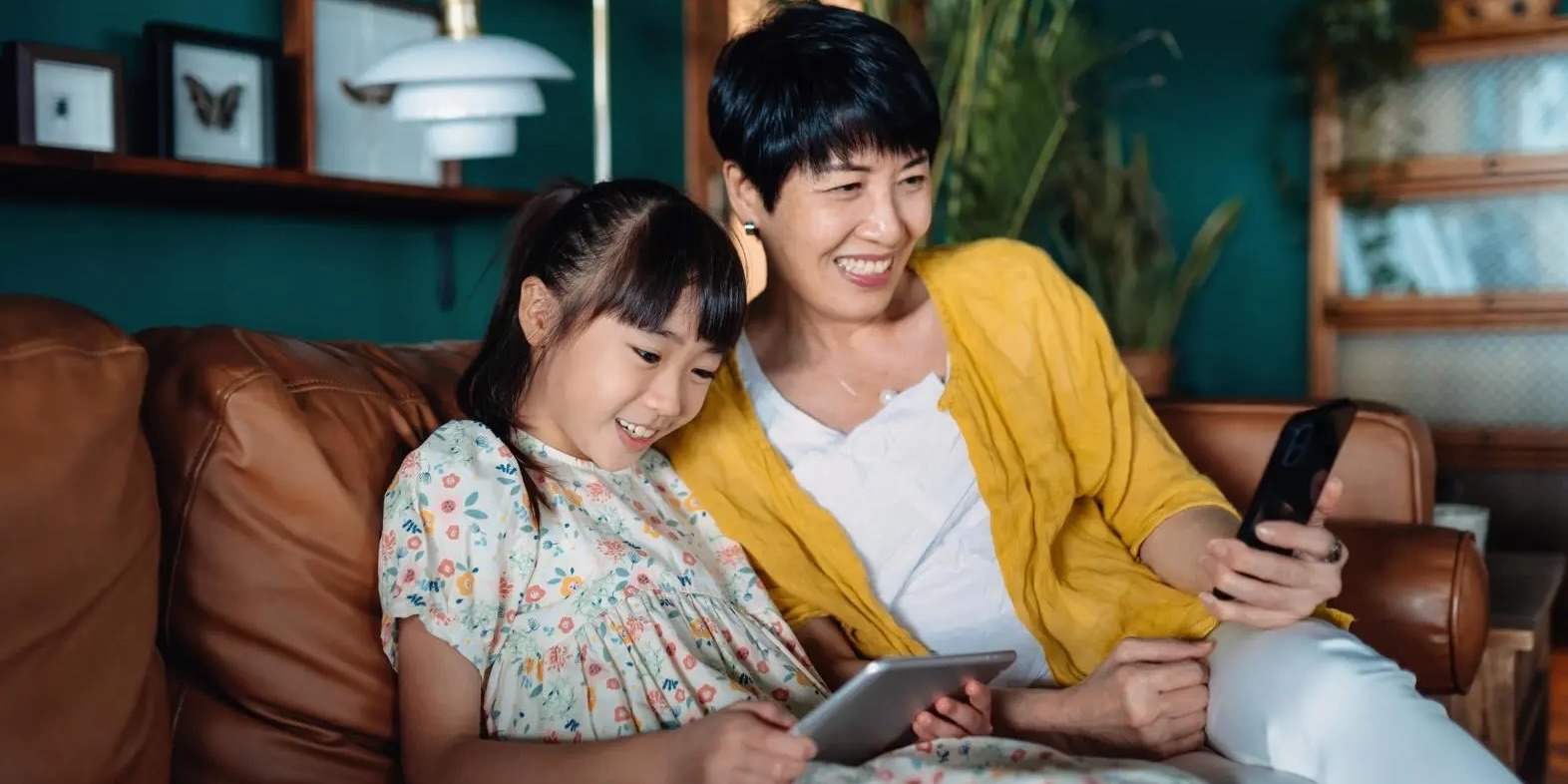
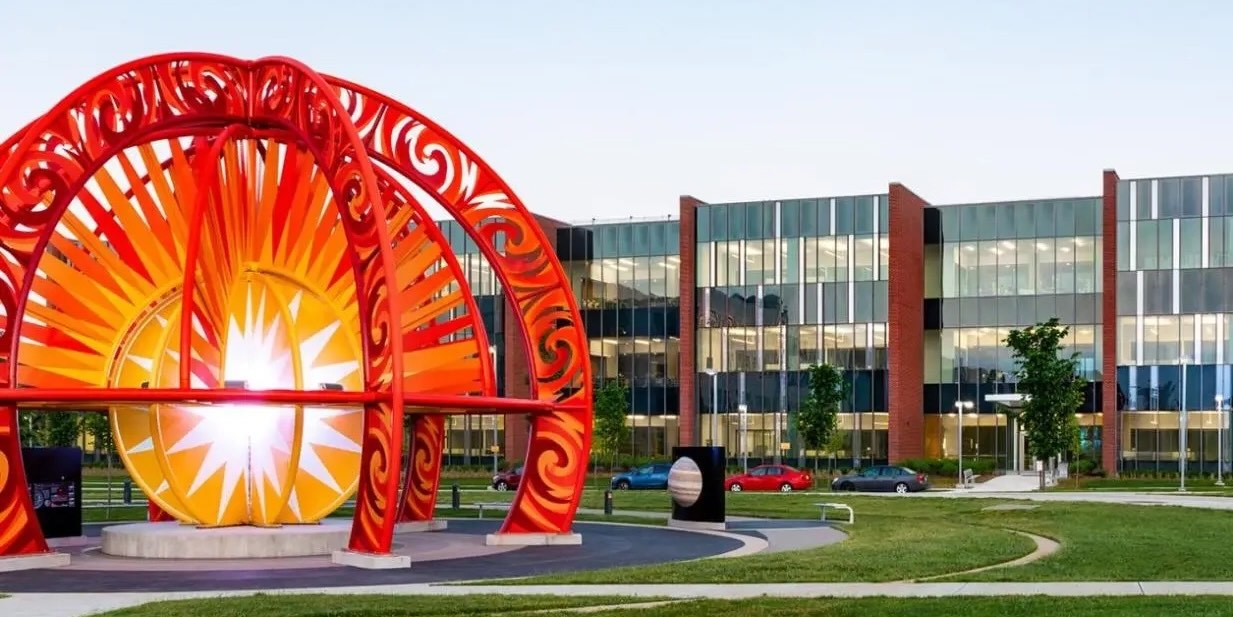
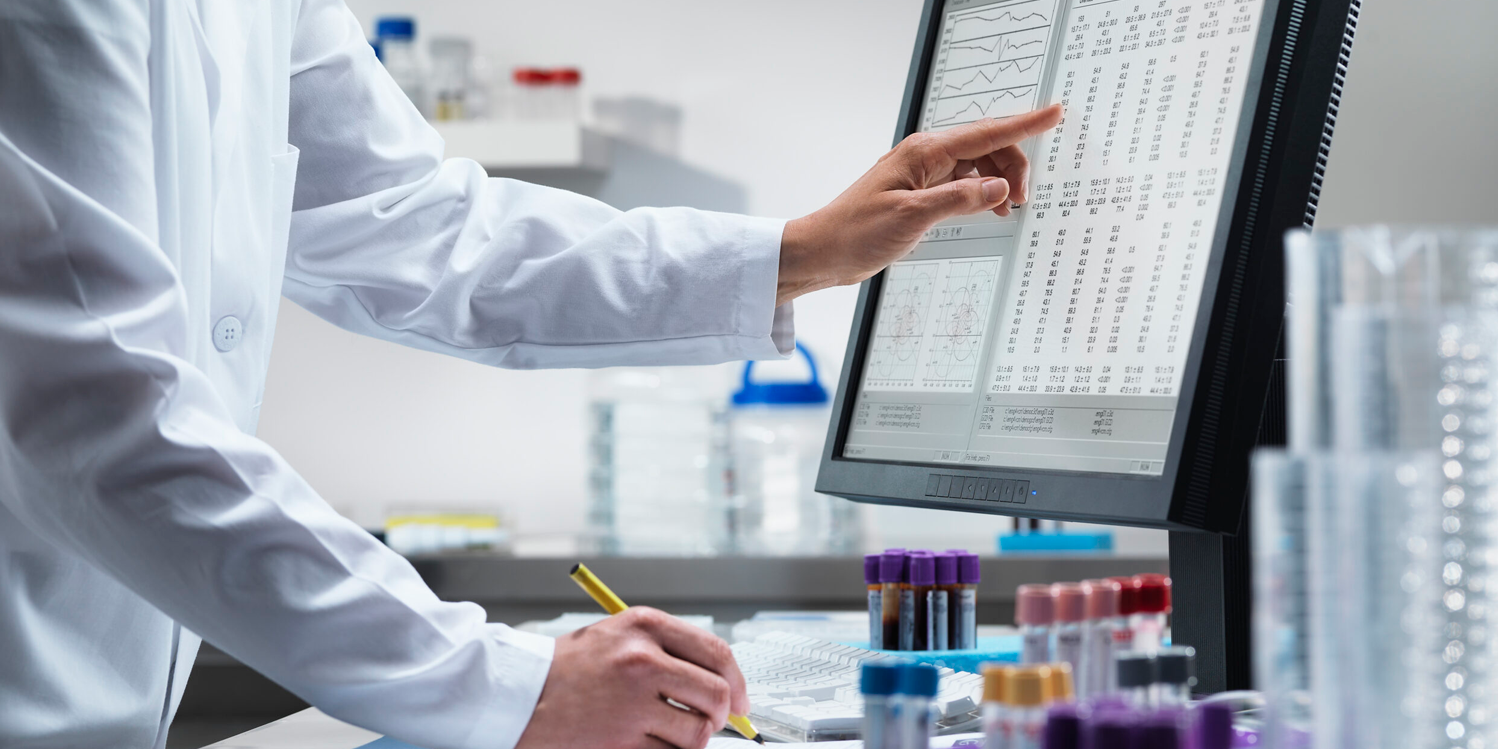
News & Featured Updates
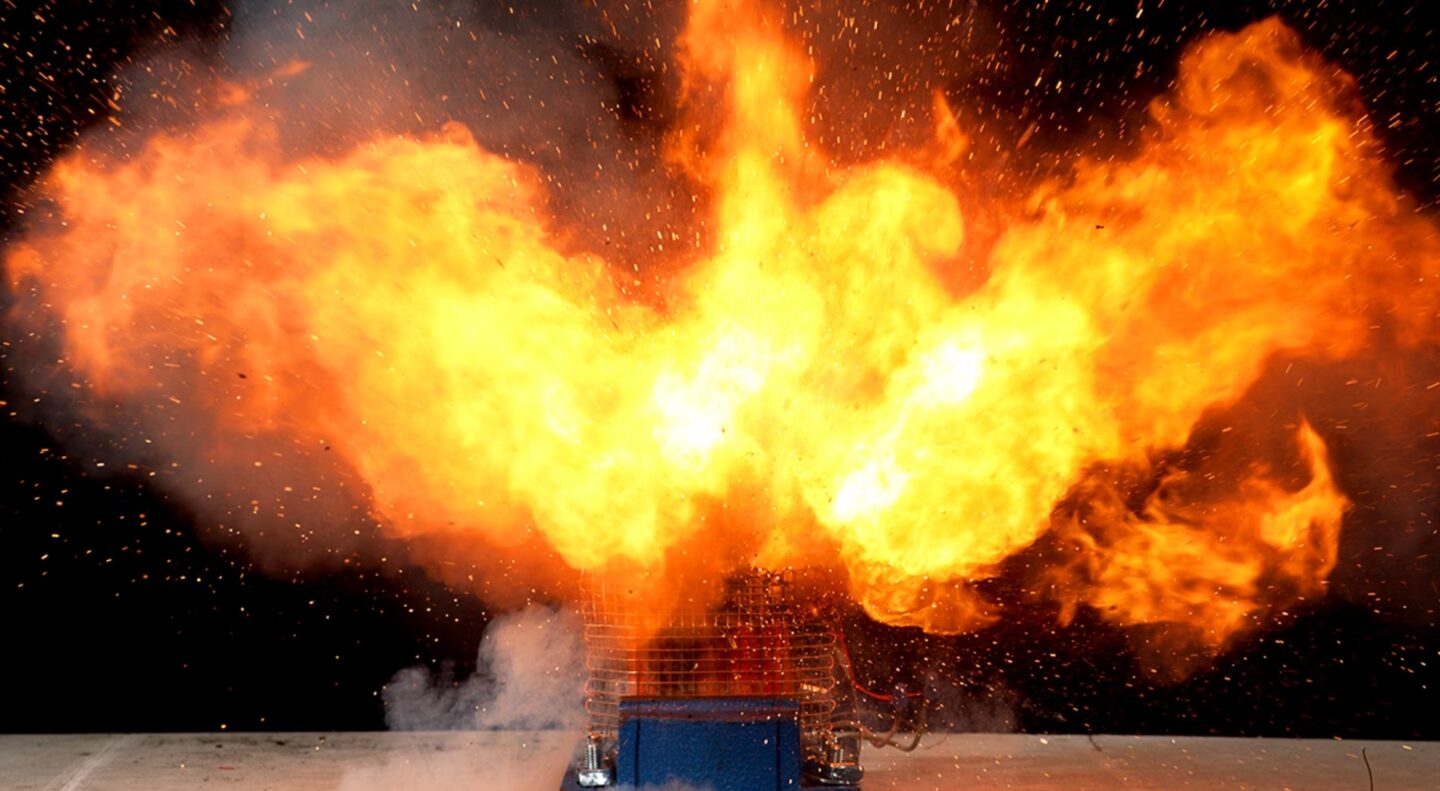
ESRI programs
ESRI Events
We bring together key stakeholders and decision-makers from a wide cross-section of the global safety community by hosting and visiting events.
Stay informed
Sign Up for Updates
Explore critical research and practical insights related to the safety and sustainability of energy storage and energy generation from the Electrochemical Safety Research Institute. Sign up to learn more about our initiatives, partnerships, upcoming events, and free resources.
By submitting this form, I am opting in to receive communications from UL Research Institutes (ULRI) containing news and updates about its work and initiatives. I understand that I can manage my preferences at any time and agree to ULRI’s online policies.
Partnerships
Everyone benefits when world-class institutions work together to take on big challenges. Join us.
Grants
We’re funding scientific research to make the world safer, healthier, and more sustainable. Learn about funding opportunities.
Careers
Work to make the world a safer place. Start a rewarding career at UL Research Institutes with other socially minded colleagues focused on innovation, collaboration, and ethics.